Additive Manufacturing '24
Topological awareness towards collision-free multi-axis curved layer additive manufacturing
Don Pubudu Vishwana Joseph Jayakody, Tak Yu Lau, Hyunyoung Kim, Kai Tang, Lauren E.J. Thomas-Seale
Additive Manufacturing. Volume 88. 25 May 2024 [pdf]
We present a topology-aware computational framework that enables global collision-free and support-structure-free material extrusion for curved layer multi-axis printing of a range of high-genus and simply connected models. The nature of multi-axis additive manufacturing facilitates continuous variation of build direction, which paves the way for numerous approaches of geometry-based curved layer design. However, due to unawareness of global topological features, prevention of collision between the printer nozzle and the workpiece can either remain uncertain or demand for exhaustive algorithmic approaches, depending on the topological and geometrical complexity of a given mesh model. In this paper, we present a topological analysis framework that draws inspiration from the concepts of Reeb graph and Morse theory, to distinguish between collision-prone and collision-free regions of mesh models. We provide an exact definition for global collision-inducing features in regions of risk and optimise the nozzle orientation vector field to avoid global collisions whilst adhering to the overhang angle constraints. A new shape analysis method is then proposed to find the model orientation which maximises the manufacturability of bifurcating simply connected models. To validate our algorithmic framework, several high-genus and bifurcating simply connected models are printed using a robotic multi-axis printer. The experimental results demonstrate the feasibility and effectiveness of our framework for minimising global collisions in multi-axis curved layer additive manufacturing for a range of mesh models.

Fig. 9. Treatment of nozzle orientation vectors: (a) Difference between average face normal vector (blue), vertex normal vector (black) and optimal vectors from our method (red) on the boundary curve of a curved layer; (b) Generated smooth vector field (green) from the optimised vectors (red) at the boundary curve.

Fig. 13. A representative bifurcating simply connected model on our framework: (a) Printed King Kong model; (b) Distribution of overhang angles with vertex normal vectors (green) and orientation vectors of our method (red); (c) Distribution of angle variation with vertex normal vectors (green) and orientation vectors of our method (red).
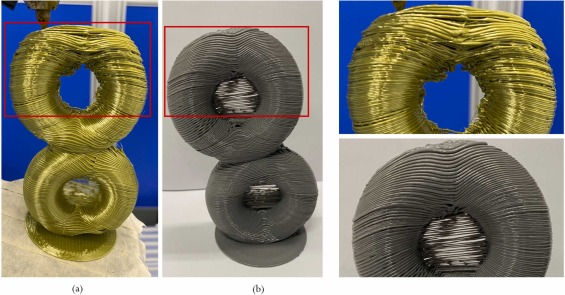
Fig. 19. The comparison of printed Genus-2 models between (a) the manually fine-tuned nozzle orientation vectors of [12] and (b) our optimised nozzle orientation vectors from a fully automatic topology-aware process.